
Inside TSMC’s struggle to build a chip factory in the U.S. suburbs
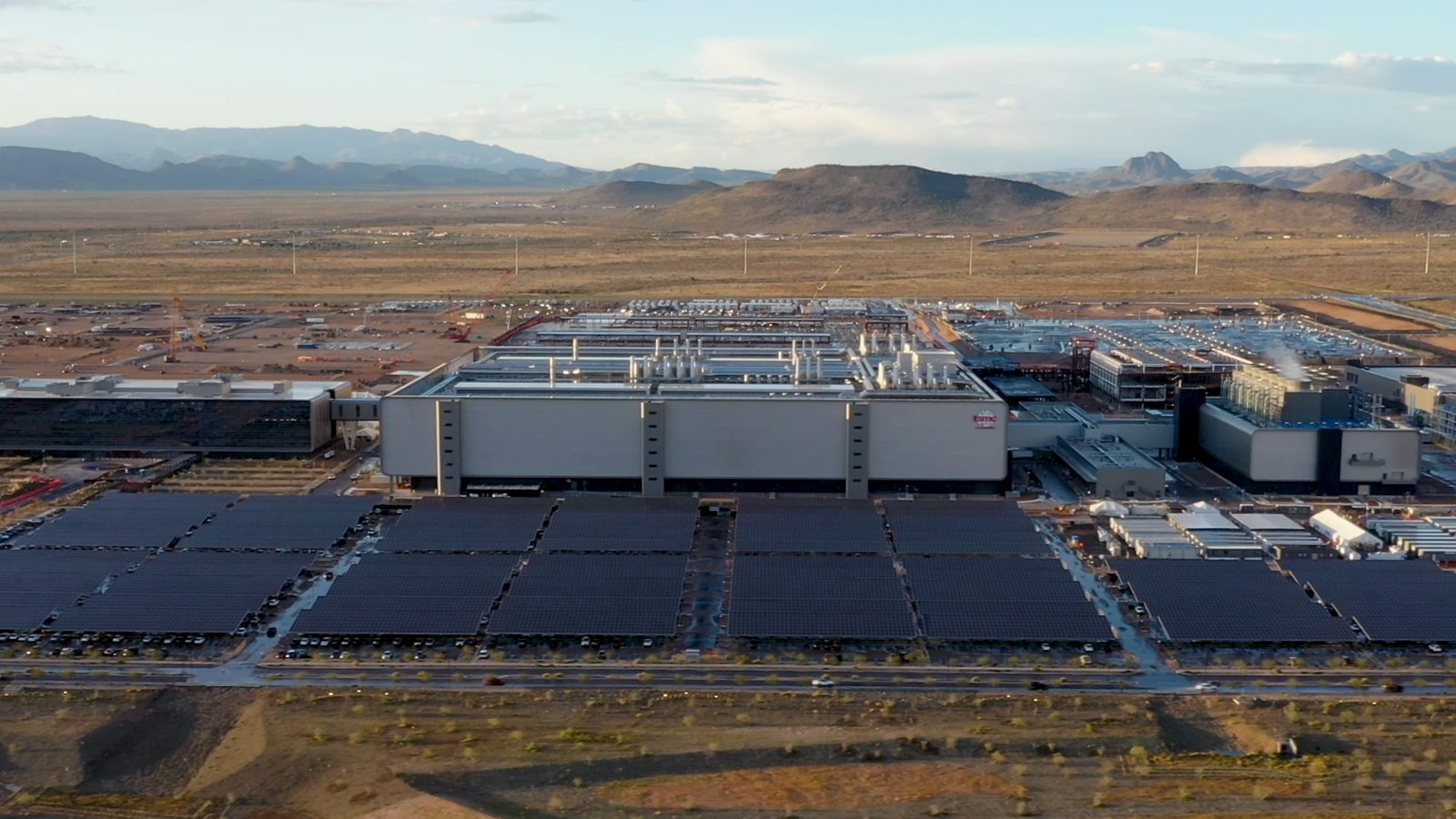
🌈 Abstract
The article discusses the challenges faced by TSMC, the world's leading semiconductor manufacturer, as it attempts to establish a manufacturing facility in the United States. It explores the cultural and operational differences between TSMC's Taiwanese workforce and the American engineers it has hired, as well as the delays and setbacks the company has experienced in getting its Arizona plant up and running.
🙋 Q&A
[01] TSMC's Expansion to the US
1. What were the key factors that led TSMC to expand its operations to the US?
- The coronavirus pandemic exposed weaknesses in global semiconductor supply chains, leading US policymakers to rally around boosting domestic chip manufacturing.
- The US government, under the Trump and Biden administrations, actively courted TSMC to build a new advanced manufacturing facility in the US, offering incentives and funding.
- TSMC saw the geopolitical importance of having a US-based facility, as the world's dependence on TSMC's Taiwan operations could incentivize the West to defend Taiwan from potential Chinese aggression.
2. What were some of the initial challenges TSMC faced in setting up its Arizona plant?
- Significant language and cultural barriers between the Taiwanese and American engineers, with communication and training in Taiwan conducted primarily in Mandarin and Taiwanese.
- Difficulties in adapting TSMC's intense, military-style work culture to the American workforce, who were less accustomed to the long hours and strict hierarchy.
- Tensions and misunderstandings between the Taiwanese and American employees, including allegations of discrimination and inappropriate behavior.
- Delays in the construction of the Arizona facility, which was originally slated to begin production in 2024 but is now pushed back to 2025.
[02] Differences in Work Culture and Expectations
1. How did the work culture and expectations differ between TSMC's Taiwanese and American employees?
- TSMC's Taiwanese engineers were accustomed to the company's rigorous, military-style work culture, with long hours, strict deadlines, and a strong emphasis on obedience and loyalty.
- The American engineers, in contrast, valued work-life balance and were less tolerant of the intense work demands, feeling that many tasks were not meaningful or necessary.
- Taiwanese managers were described as creating a "false sense of urgency" and expecting immediate completion of all tasks, while the American workers preferred a more measured approach.
- There were also differences in communication styles, with the Taiwanese engineers more comfortable with hierarchical decision-making and public criticism, which the American workers found unacceptable.
2. How did TSMC attempt to bridge the cultural differences between its Taiwanese and American employees?
- TSMC provided some cultural training for the Taiwanese workers, teaching them about American work culture and the importance of encouragement over criticism.
- The company also loosened restrictions on the use of personal devices and social media to help the American workers feel more comfortable.
- TSMC made efforts to improve English-language communication, holding classes for Taiwanese managers and reminding them about inappropriate language use.
- However, many of these attempts were seen as insufficient, and the cultural divide remained a significant challenge for the company.
[03] Delays and Setbacks in Arizona
1. What were the key reasons for the delays in getting TSMC's Arizona plant operational?
- A shortage of skilled workers, which TSMC blamed for the delays, though construction unions suggested safety issues and the use of cheap Taiwanese labor as potential factors.
- Ongoing language and cultural barriers between the Taiwanese and American employees, which hindered effective collaboration and decision-making.
- Reassignment of engineers to work remotely for TSMC's Taiwan operations, pulling resources away from the Arizona plant.
- Engineers being asked to take on non-technical tasks like overseeing construction workers and collecting trash, rather than focusing on production.
2. How did the delays in Arizona compare to TSMC's success in opening a new facility in Japan?
- TSMC was able to open a new factory in Kumamoto, Japan in a much shorter timeframe of around two years, thanks to strong government support, local partnerships, and a 24/7 low-cost labor force.
- The news of the Japan factory's rapid completion prompted feelings of envy and frustration among the engineers working on the delayed Arizona plant, who felt they were falling further behind.
- Some Taiwanese engineers at the Arizona plant complained that TSMC was being too accommodating of the American workers, while others acknowledged the challenges of bridging the cultural divide between the two workforces.
[04] Broader Implications and Outlook
1. What are the broader implications of TSMC's struggles in establishing a successful US manufacturing presence?
- The difficulties TSMC has faced highlight the challenges of transplanting the company's Taiwanese-centric work culture and operations to the US, where the workforce and regulatory environment are quite different.
- Experts suggest that TSMC's profits from its US facilities may be lower than its Taiwan operations, unless customers are willing to pay more for chips produced in the US.
- The US still has a long way to go before achieving chip self-reliance, as the TSMC Arizona plants will only produce a fraction of the company's global capacity, and many chips still need to be shipped back to Asia for final assembly and packaging.
- Sustained, consistent government support and the development of a robust domestic semiconductor ecosystem will be crucial for the US to truly reduce its reliance on foreign chip suppliers like TSMC.
2. What is the overall outlook for TSMC's success in the US market?
- There is skepticism among industry analysts about whether TSMC can fully replicate its Taiwan-based success and efficiency in the US, given the cultural and operational challenges.
- The company's ability to bridge the gap between its Taiwanese and American workforces, and to adapt its management practices to the US context, will be critical to the long-term viability of its US operations.
- The significant government incentives and funding provided to TSMC and other semiconductor companies suggest the US is committed to supporting the domestic chip industry, but the path to true self-reliance remains uncertain.